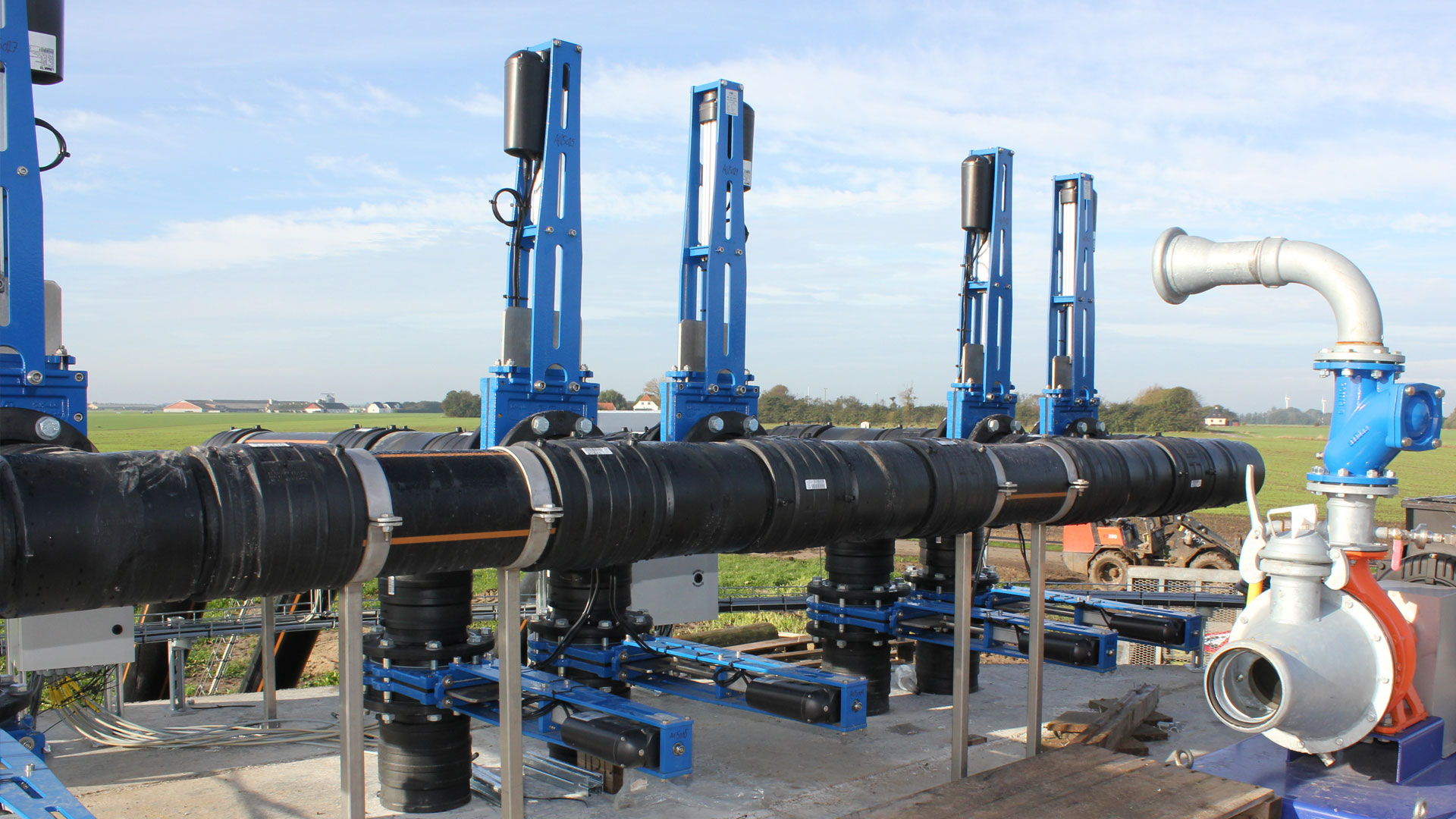
Degassing slurry in a biogas plant before it is spread in the field means, among other things, less odor nuisances, higher fertilizer value and less impact on climate.
A Danish farmer running a large pig farm and a biogas plant has invested DKK 14m in a pipe system to transport the slurry from local farms to the biogas plant and back to the fields where the degassed slurry is to be spread out. Knife gate valves are fixed on manifolds between the farms and the biogas plant to safeguard that the slurry is transported to the right places. Automated control of opening and closing the valves ensures that the slurry can be pumped in both directions in the system.
Pipe system for transporting slurry reduces traffic load
The farms being allied to the new pipe system save both time and operating costs. In addition, launch of the system will also decrease the traffic load and the challenges related to this. Slurry tankers no longer need to drive back and forth between the farms and the biogas plant, and by launching buffer tanks and taps at the fields, the need for driving back and forth between the fields and storage tanks on the farms is also minimized.
Nearly 20 km of pipes connect ten farms, a pumping station and the biogas plant, which processes up to 160,000 tons of biomass per year, and the pipe system results in a significant decrease of the traffic load.
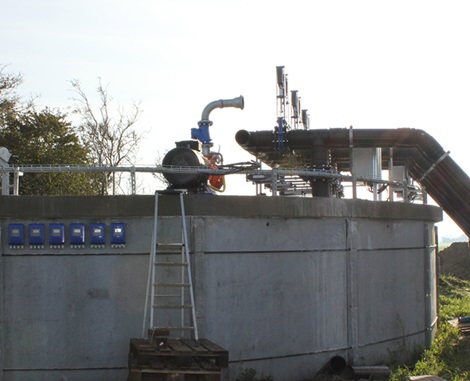
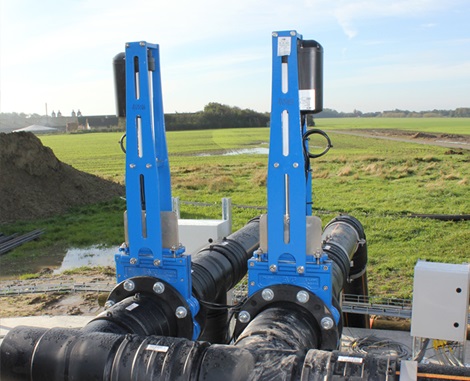
Degassing results in less impact on climate and less odor nuisances
Slurry is pumped from the farms for degassing in the biogas plant, and then it is pumped back to the farms for storage in tanks directly by the fields. Degassing slurry before spreading out has several advantages. The degassed slurry provides a higher fertilizer value and results in less odor nuisance and reduced methane emissions. Methane is a greenhouse gas that negatively impacts the climate far more than CO2, and thus the degassed slurry has less impact on climate.
Pipe system with 26 pcs. DN200 knife gate valves
The pipe system is dimensioned with 200 mm PE pipes and for a maximum pressure of 10 bar. Vatech 2000 has delivered 26 pcs. Electrical actuators have been chosen because the valves are installed over a large area and to allow for feedback modules, which can provide an overview of the actuator settings.
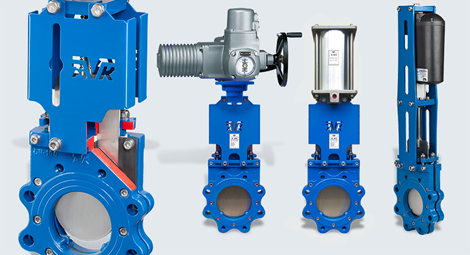