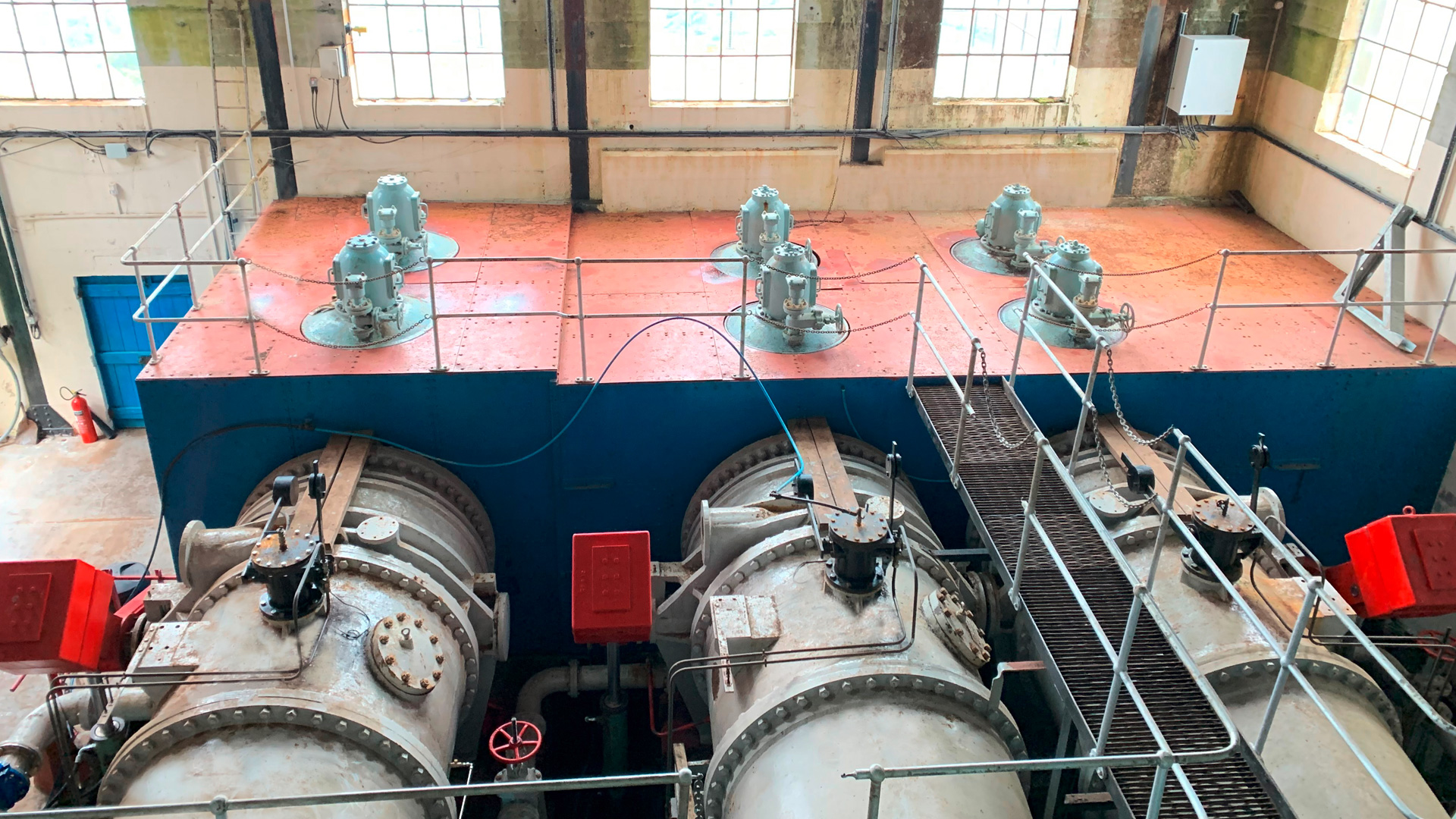
The location some 1,000 ft above sea level, extreme weather and tight manufacturing timescales made Kinlochleven a challenging and exciting replacement project
Challenging conditions
Access and potential exposure to interesting weather events were two of the key challenges facing the customer and Glenfield Invicta on the Kinlochleven project. The penstocks themselves are nearly 1,000 feet above sea level and nearly 142mm (5.6 inches) of rain fell in one 24-hour period during the system's initial construction.
Given the location and weather the customer preferred that the work be completed in single visit. This in itself was a challenge with the penstocks in three different locations and a short manufacturing time from drawing approval to start on site. Compounding all of these hurdles was the Covid-19 lockdown. During the national lockdown, the project was awarded, manufactured, and installed.
Hydropower: an international perspective
The UK has 4,700 MW of installed hydropower capacity; which is a massive amount of energy, when you consider that with just 1 MW can power an average home for more than a month. The vast majority of this capacity is located in North Wales and The Highlands of Scotland.
Interestingly, hydropower was used to generated electricity for the first time in Scotland in 1879, two years before the first public electricity generator.
To provide an international perspective, China has nearly one hundred times more installed hydropower capacity than the UK. According to the International Hydropower Association, Denmark has only 9 MW, the smallest installed capacity of any major European country with the exception of Estonia.
Almost 100 years old and still in operation
Glenfield Invicta visited the site and discussed the issues that needed to be addressed. Glenfield Invicta had previously worked on the Kinlochleven and the current penstocks dating back to the 1930s were manufactured by Glenfield. This pedigree, reinforced by a rapid response and a scheme of works that required only one visit to site, led to Glenfield Invicta being awarded the works. The general arrangement (GA) drawings quickly followed, and customer approval enabled the manufacturing process to begin.
From manual to remote operation
The penstocks were made of stainless steel and equipped with electric actuators to enable remote operation; which was a significant improvement over the manual operation of the legacy penstocks.
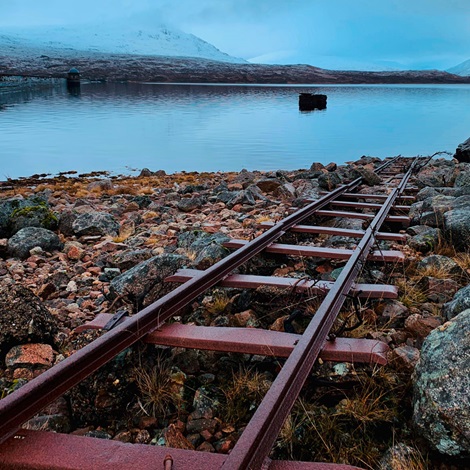
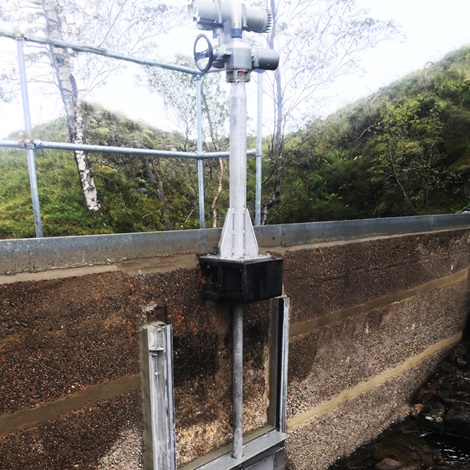
The scheme’s history
The Alvance Aluminium smelting works based at Fort William is the last one of its kind in the UK. Aluminium smelting is energy intensive as the process requires alumina (aluminium oxide) to be dissolved in synthetic cryolite at 1,000ËšC. The only commercial deposit of the mineral cryolite was in Greenland, but this has now been exhausted.
The Fort William smelting works draws the majority of its power from two hydroelectric schemes: the Lochaber hydroelectric scheme commissioned in 1929 and built specifically for the works, and the Kinlochleven hydroelectric scheme, originally built to supply power to a now non-existing smelting works. Both schemes are now operated by Alvance’s sister company, SIMEC, and in their day were major civil engineering projects.
The Kinlochleven scheme is fed by the Blackwater river’s chain of creeks. The Blackwater dam, the longest dam in the Highlands at 948.5m, was constructed in the first decade of the 1900s to create a reservoir.
Water from the reservoir is transported via a 5.6km long concrete conduit and subsequently into steel pipes that feed the water into the power station turbines. The flow of water into the conduit and pipes is controlled by three DN1000 penstocks. These were originally manually operated.
Made by hand
The Blackwater dam is located in almost inaccessible terrain. Amazingly, the dam was constructed using hand tools by over 2,000 manual workers, without the benefit of mechanical earth moving machinery. Materials were transported to the site from the wharf at Loch Leven via a 10.5km cableway.
Great team effort
The installation was undertaken by Glenfield Invicta’s full-time penstock installation team, which made it through on time despite significant flooding during the week of the installation.
The works themselves were quite challenging as cofferdams had to be created and water pumps used, to divert the flow of water. A cofferdam is an enclosure built within a body of water to allow the area to be pumped out. This creates a dry working environment so the work can be carried out safely.
Peter Dodds (Mechanical Engineer at SIMEC) was delighted with the attitude of the team and their drive to get the job done without a need for a second visit:
“The installation team were great to deal with and helped overcome all problems such as the unexpected rainfall which tested the pumps and cofferdams. The newly installed penstocks have been a great improvement in terms of operation, leakage, and improved safety for our operators.”
Wilson McPhail and Jim McAllister, Glenfield Invicta’s leads on the project, add:
“The success of the project can be put down to three key factors. Firstly, the customer trusted our expertise and allowed us to get on with the job. Secondly, open communications and teamwork helped smooth project delivery. Finally, the positive attitude of the Glenfield Invicta workshop and installation teams meant we were able to absorb everything that the weather had to throw at us – and it was very wet! – and still complete the works within the narrow time window available to us.”